In Part I of our Series on Deaerators, we discuss the “why and how’ deaerators are employed to protect the boiler system while saving energy and chemical costs. In this article, we want to address how to keep deaerators effective in corrosive gas removal, and reliable with their ongoing support of the system.
There are three (3) aspects you need to consider: Monitoring, Maintenance and What If.
MONITORING
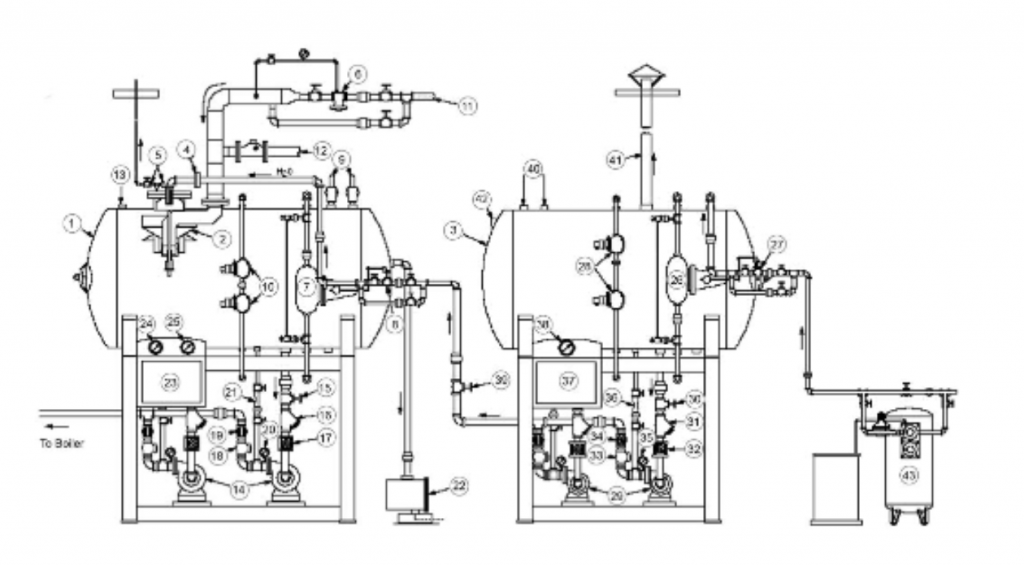
Figure #1
Monitoring begins with the assurance you have accurate gauges for checking pressures and temperatures in the deaerator. This can mean using analog or digital instruments, but they must be accurate. For instance, if you check an operating deaerator with a pressure of 5 psig, the thermometer should read 227 deg. F. If either one does not match pressure with its equivalent saturated temperature as found in a steam table, one is wrong and recalibration or replacement of the instrument will be necessary.
It is also a good idea to have a thermometer in the supply line to the DA before it enters the tank itself; monitoring it for a consistent feed temperature be it cold 100% raw makeup or a warm blend of condensate return and makeup. Deviation from the blended norm indicates a supply problem and it needs to be addressed.
Assuming the instruments are all accurate, check the pressure in the deaerator (DA) frequently throughout the day to make sure the desired pressure is being maintained. If it is lower than desired, and the boiler has not deviated from its normal working pressure, the problem is often with the pressure reducing valve (PRV) regulating the steam supply from the boiler. This will need to be adjusted or replaced as necessary.
If the problem is a higher pressure in the DA, there may be a bad steam trap(s) in the supply line causing steam to “blow-by,” backing up condensate into the steam supply line. This steam/water mix at a very high traveling velocity will wiredraw the PRV’s heads and seats; affecting its regulating ability, causing the pressure to rise on the DA.
At the same time, you’re checking the pressure in the DA, and as previously mentioned, you’re also checking the equivalent temperature with an accurate temperature gauge. If the temperature is lower than the saturated pressure in the DA, this often points to a problem with the DA’s deaerating internals.
As soon as possible when seeing this condition, the DA needs to be isolated, drained and inspected to determine the cause (See Maintenance below). Often a trained technician is required to diagnose, repair or replace the faulty component(s).
The next monitoring point is checking the water level in the deaerator’s tank. This level may be visualized with the equipment furnished with the unit be it an electronic indicating device or a gauge glass mounted on the DA’s water level controller. High or low levels can be indications of excessive or inadequate condensate return, a problem with the modulating control valve, etc. It needs to be diagnosed and remedied as soon as possible to prevent damage to the boiler and/or deaerating equipment.
Lastly, with Monitoring, the boiler operator needs to frequently check the Sulfite level in the DA tank. This, because the DA tank is most likely constructed of carbon steel, and though the DA is there to remove corrosive gasses, there will still be some residual traces of oxygen and the sulfite will scavenge these traces, protecting the tank. Also if you find the sulfite level to be very low, that’s an indication the DA is not doing its job effectively, allowing O2 levels to climb. Again action needs to be taken promptly to determine the cause and correct it. Failure to do so will ultimately cause damage to the boiler and the DA itself.
MAINTENANCE
A deaerator needs to be isolated, drained, opened and cleaned on an annual basis; normally at the same time as the boiler.
IMPORTANT NOTE about the DA’s internal components which are constructed of stainless steel….This material can corrode; differing from commonly held belief. Stainless steel is comprised of carbon, iron and chromium which forms a chromium oxide layer making it resistant to normal corrosion. However, the chemical reaction of this oxide layering can be disrupted with the presence of ferritic deposits from iron and steel coming from the DA tank or connected piping, and leading to a rust like corrosion. Another possible cause for stainless corrosion is sodium in the feed water coming from the water softener which isn’t going through the proper rinse cycle. These sodium deposits can form corrosion pits in the stainless, shortening its durable life.
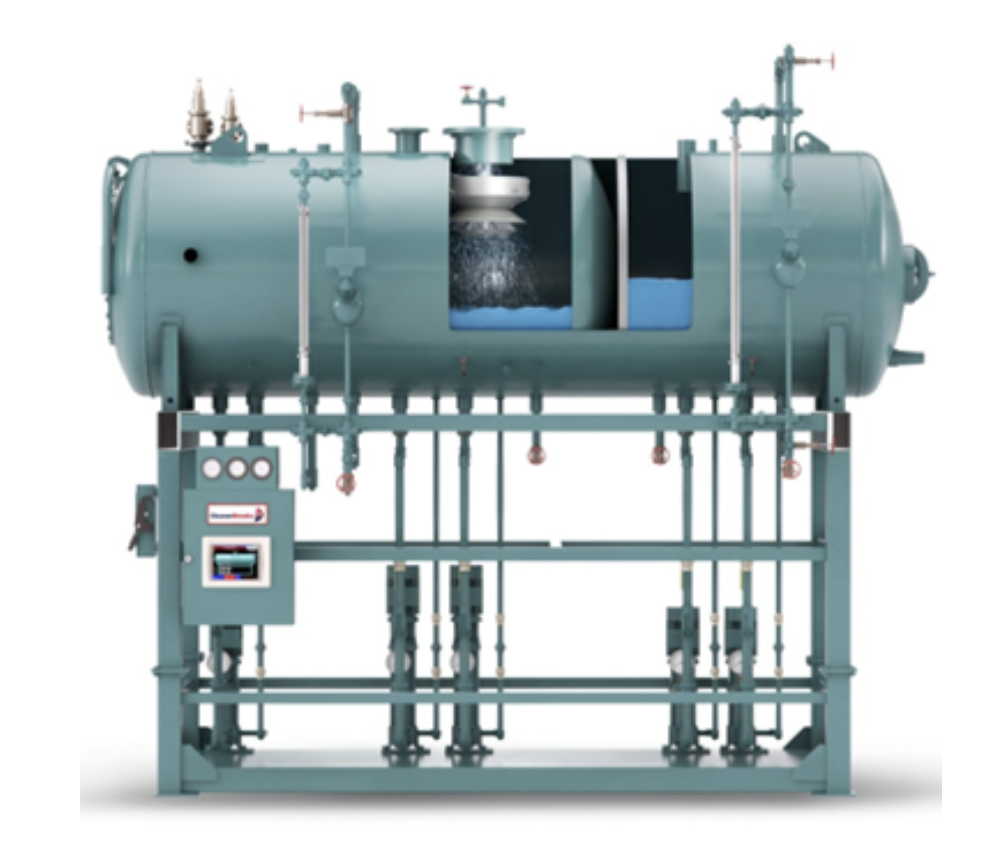
Figure #2
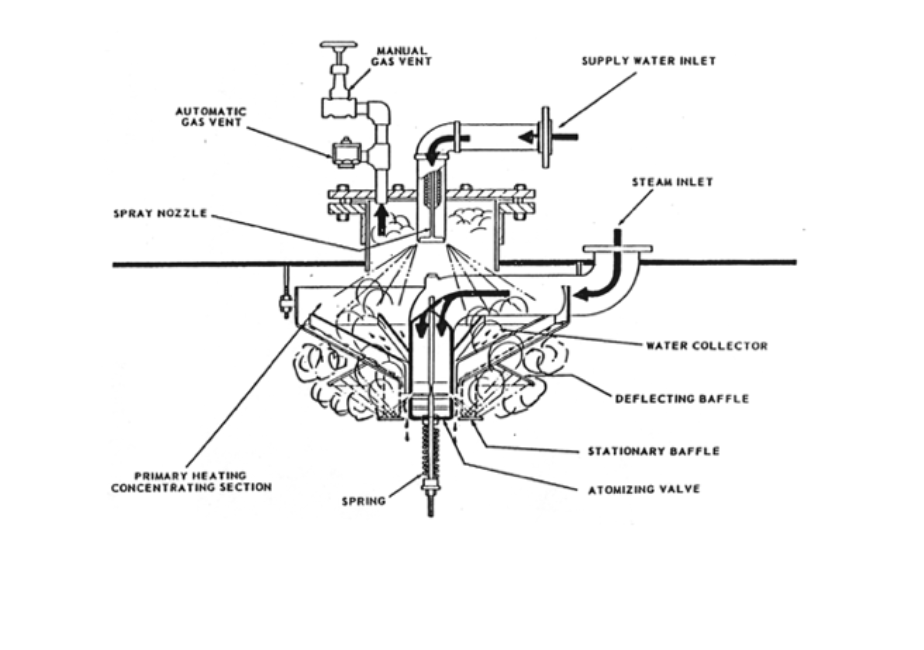
Figure #3
Referring now to Figure 2, you see a Spray-type deaerator including the spraying assembly. Looking now at Figure 3, you find a closer look at the spray assembly and including the steam atomizing valve and water collector both of which need to be closely inspected for any signs of corrosion or deformation. At this time you are also checking the condition of the self-cleaning spray nozzle. If scale is present, the assembly needs to be removed and cleaned. This will include reinstallation of the spring which needs to be replaced with the exact tightening as prescribed by the manufacturer. Again, a qualified technician’s assistance would be very desirable at this juncture, assuring proper compression and tightening of the spring.
At this time you are also looking for any scale or other deposits in the tank itself, and if found, it all must be completely removed.
Next, we want to check the condition of the float operated water level control. It needs to be removed and inspected, and if needed, cleaned of any scale or mud. It is also at this time when the cross-connecting piping needs to be inspected and “rodded” free of any obstructing debris. Also, the gauge glass needs to be inspected and replaced if any signs of thinning or etching are found. This includes replacing the gaskets as well.
The pumps are the next area to be inspected. Start with the suction piping assuring the strainer is clean and no obstructions are present in the piping. The pumps themselves should be free from any evidence of seal or piping leaks on both the suction and discharge sides. Also any signs of motor overheating. Take appropriate action as required.
Lastly, check the water softener for proper salt level and operation by manually taking it through the various operational cycles. Pay special attention to the brine draw and rinse cycles for reasons stated earlier.
The other two DA types (Column & Tray) will follow the same maintenance procedures as with the Spray type; however, special attention should be paid to the stainless steel trays (Fig.4) in the Tray type. Normally, these require removal to assure no corrosion or scale deposits have formed on them.
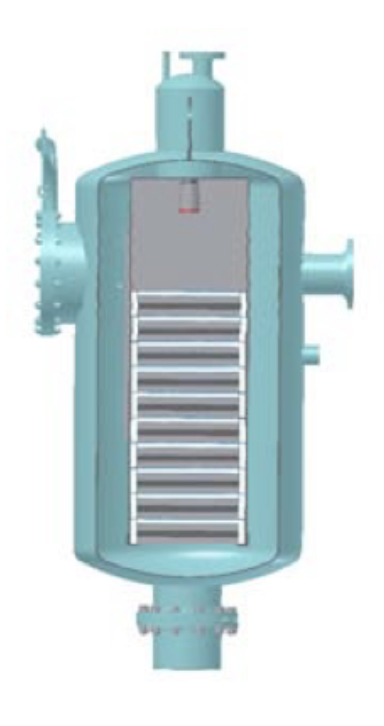
Figure #4
WHAT IF?
What if you have a deaerator which needs major attention requiring it be down for an extended period of time, and the process needs to come back online?
In many cases, companies have a Surge tank connected to the DA which automatically
supplies a blend of condensate and boiler makeup water; using its own pump for supplying the DA with the water it needs to deaerate for the boiler.
In addition to feeding the DA, the Surge tank’s other main function is being a reservoir for handling volume swings in the condensate returns based on varying load and seasonal changes. Without this tank, it is often the situation where the surge capacity within the DA itself would be exceeded necessitating costly condensate waste.
Now having a Surge tank for this purpose, it can be readily modified to include a dedicated pump for feeding the boiler; properly sized for the total evaporation rate of the unit with sufficient safety factors figured in to account for adequate flow including pressure drops, line losses, and sufficient discharge pressure (TDH) to allow enough water to enter the unit. These calculations will vary based on on-off or continuous pump operation which in the continuous pumping case, will require a by-pass line to the Surge tank.
The NPSHR for the pump will also have to be checked, allowing for adequate suction pressure based on the expected inlet water temperature.
Special piping is then installed to feed directly to the boiler with appropriate valve connections in place to isolate or open it if the DA is down for maintenance, and the boiler needs to be fed to support the process.