Businesses are continually looking for ways to save money and reduce cost. The boiler room offers unique boiler upgrades and retrofit opportunities that cannot be overlooked.
Boiler operation accounts for a high percentage of the fuel cost when looking at the facility’s overall cost of operation – many times burning in excess of 4 times its initial cost in fuel annually. When looking at ways to greatly mitigate this cost, there are a number of areas one can look at for relief, and it all starts with the following priorities:
The Pressure Vessel
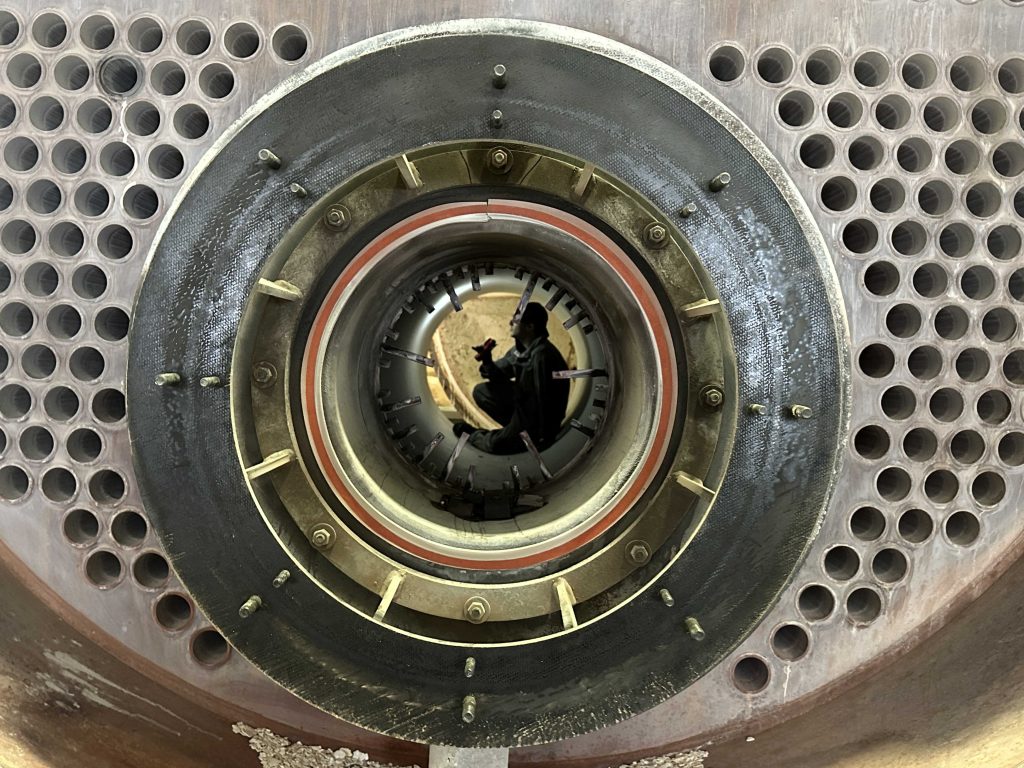
Pressure Vessel Inspection
Begin with closely evaluating the boiler’s pressure vessel regardless of age, to determine if it still has years of life in it. In other words, closely look at
metal and weldment integrity, any large deposits of scale, signs of leaking or metal corrosion. This close inspection can all be done during the boiler’s annual shutdown and draining. If all things are positive, and the vessel is in good shape, proceed to the burner.
The Burner
A burner evaluation starts with a qualified technician inspecting and testing the burner to make sure it properly tracks through its modulating range and combusts without excessive O2, and CO, shutting down and purging both pre and post firing. If it does not, and it can’t be confidently adjusted, replace the burner with one which meets the application needs, and matches the furnace in which it is firing. This is most important because it’s the furnace that provides the TIME for combustion to complete.
Things to consider for both a new or existing burner; reducing the fuel spend:
- Include parallel positioning actuators for fuel and air regulation, replacing single-point positioning linkages. An efficient burner provides the proper air-to-fuel mixture throughout the full range of firing, without constant adjustment. Many burners with complex linkage designs do not hold their air-to-fuel settings over time. Often, they are adjusted to provide high levels of excess air to compensate for inconsistencies in the burner’s modulation. This high excess air costs extra fuel dollars. For an alternative to these complex linkage designs, install servomotors with parallel positioning to independently control the quantities of fuel and air delivered to the burner head. This control system allows for easy tune-ups and minor adjustments while eliminating hysteresis, or lack of repeatability; delivering accurate point-to-point control while saving many fuel dollars annually.
- Boiler “short cycling” occurs when a boiler quickly satisfies the process and/or space heating demand, and then shuts down until heat is again required. This results in numerous pre and post-air purges of the furnace for safety reasons, literally blowing countless Btu’s out the stack; driving up needless fuel costs. Energy losses of 15% are not at all uncommon when cycles exceed ten (10) per hour. The solution to this problem is retrofitting or specifying in the case of a new burner, a High Turndown Burner with 10:1 turndown capability.
Burner Retrofit
In addition to this solution consideration, the boiler may also be oversized for the load especially during certain months of the year when specific loads such as comfort heating are shed. In this case, it would be wise to consider another smaller boiler (new or used) be employed at this time to not only mitigate cycling losses but also allow the boiler to operate and fire at its most efficient point which in most boilers is above 85% of its rating.
- Another retrofit consideration making cent$ is the use of a good Oxygen Trim system. As you know, a burner needs fuel and air to combust, and the combustion air fan delivers air at a specific rate regardless of the changing conditions in the boiler room. This means when the boiler room gets colder the air gets more dense. As the room heats up, it gets less dense. This means if the fan discharge is not regulated to account for
Advanced Controls Upgrade
these density changes, the burner can go from excessively high excess air (loss of energy) to excessively short of air; forming dangerously high CO levels and possibly explosive unburned carbon. The O2 Trim system accounts for these changes, automatically adjusting the air damper or fuel valve to account for the irregularities. This retrofit saves energy dollars and greatly improves safety.
- Is there an alternate waste fuel in your facility which could be burned or are you close to a landfill or digester gas facility? These fuels can be burned in a properly designed and controlled burner. Many times your local Utility will offer discounts for going “off-peak” while also assisting in the retrofit cost. It’s worth checking out…
- The next thing to look at is the Operating Controls on the boiler (operating, modulating and high-limit controls). Are they old? If they are, it would be wise to check their settings against the actual pressure or temperature in the boiler to see if they are actually shutting the boiler’s burner off and turning it on at the proper point. Many times they may be causing the boiler to overshoot the desired pressure/temperature point or undershoot it causing a needless loss of energy and/or process/comfort heating problems. If this is the case, retrofit new operating controls on the boiler; saving energy while improving the desired outcome in the facility.
- The last priority for saving fuel dollars is the Automatic Stack Damper. As mentioned when discussing pre and post-purge losses, it is the air blowing through the boiler when the burner is not firing which causes needless boiler cooldown and energy loss. The same is true for excessive stack draft occurring when a “live” boiler is offline awaiting the firing command from its burner management system. An automatic draft control can save this loss, closing the damper during the boiler’s off-cycle then automatically opening it again when the boiler is called to come online. Many energy dollars are saved with this feature, and it must be considered when draft exceeds approximately 2” WC. Also in this case, the auto damper control will regulate the pressure at the vent stub during firing, assisting in keeping the burner’s air/fuel ratio in the proper range at all firing rates.
It all makes good economic cents!
Contact Energy Control for a boiler room evaluation to identify cost-saving opportunities you can benefit for years to come.