Optimize condensate processes in your boiler system to improve plant efficiency. Pumping stations recover and transport condensate in order to recycle heat energy and water resources.
Why do I need a TLV Pumping Station?
Energy recovered from condensate reduces boiler fuel costs and reduces water treatment costs. The snap-action mechanism rapidly switches between condensate in-flow to the mechanical pump and discharging the condensate, preventing delay-induced leakage of motive medium – steam and air.
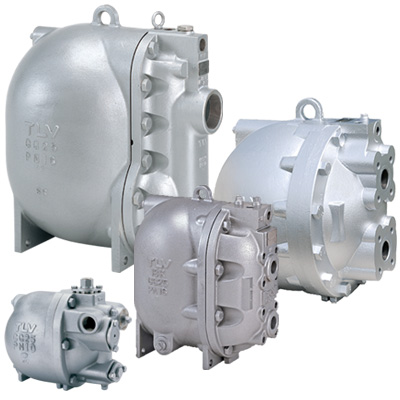
TLV PowerTrap
‘Stall’ Prevention
The steam-using equipment installing the control valve has a tendency to stall, resulting in process temperature swings, water hammer, and/or tube corrosion.
By installing PowerTrap®, this stall phenomenon can be prevented.
Easy to Operate
- The unit is powered by steam or air, so there is no need for electrical facilities, which makes it suitable for use in explosion-proof installations and other environments where electrical power supply is not an option.
- Designed to allow maintenance without being removed from condensate recovery lines.
- Unique snap-action mechanism instantaneously opens or closes the motive medium inlet and exhaust valves. This prevents leakage of the motive medium and erosion of the valve/valve seat that tends to occur with crank mechanism pumps.
- Stainless steel internal parts and durable compression coil spring.
Applications:
- Capable of being used on both closed-loop and open-loop systems
- Great for capturing pressurized condensate
- Re-Boilers and large heat exchangers
- Small to medium process flows
- Dryers, presses, autoclaves
Discharge capacity:
Discharge Capacity ranges from 300 lb/hr to 20,000 lb/hr of condensate.
Case in Point:
A local manufacturer using presses for molding was struggling to remove condensate from the presses. The current scenario was slowing down the production line. Energy Control recommended and installed (2) TLV Pumping stations. The newly installed pumping stations have reduced the presses’ heat-up time and cycle times, thus, making the system as a whole more efficient.