Various industries around the world require energy to carry out the products and services we require daily. When looking at the carbon footprint of a facility, the boiler room is typically one of the greatest energy consumers making it an obvious choice to identify areas of energy and emissions reduction to create a sustainable boiler plant.
As experts in total boiler room solutions, we will outline solutions and steps you can take to reduce energy and your carbon footprint. We at Energy Control are here to help you achieve your sustainability goals.
There are 4 areas to break down the strategies for sustainability.
- Decarbonization
- Renewable fuels
- Energy efficiency
- Emissions Reduction
Sustainability Solutions:
Decarbonization
Reduce or eliminate carbon dioxide output.
- Electric and Electrode boilers are 100% local emission-free meaning zero carbon footprint. Electric boilers are nearly 100% efficient, meaning all energy delivered to them is converted to steam or hot water. Learn about all the options for Electric and Electrode boilers here.
- Heat Recovery Steam Generators for supplemental and/or fresh-air fired applications feature a Natcom duct burner and a control system that deliver the highest efficiency and lowest emissions. The Cleaver-Brooks HRSG achieves >80% efficiency compared to 56% for traditional technologies. It reduces up to 7.0 MMBtu/hr of fuel in conventional boilers and eliminates 2,870 tons of CO2 emissions annually per 1 MWe GT output.
Renewable Fuels
- Growing pressure to lower emissions and replace fossil fuels is leading companies to explore a range of biofuels such as ethanol, biodiesel and biogas. Unlike fossil fuels, which are limited in supply, biofuels are produced from renewable feedstocks and can be sustained indefinitely.
If you have access to an alternate waste fuel in your facility that could be burned or you are close to a landfill or digester gas facility, you could be updating your burner from a fossil fuel to a renewable one. We offer dual fuel burners, which are popular with end-users that produce a renewable fuel as a by-product.
Energy Efficiency
Strategies to Increase energy efficiency by reducing waste and greenhouse gas emissions for a sustainable boiler plant.
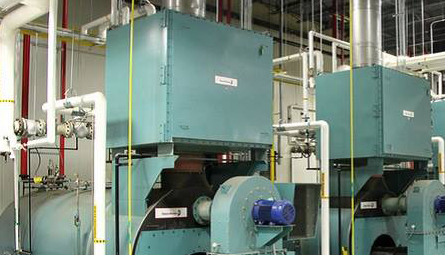
Stack Economizer for Heat Recovery
- A Stack Economizer economizer captures and redirects sensible heat from the hot flue gas that normally goes up the boiler stack. This sensible heat increases the temperature of boiler feedwater or makeup water. On average, adding a standard economizer increases boiler system efficiency by 3 percent to 5 percent.
- A Condensing Economizer captures both sensible and latent energy from the flue gases leaving the boiler. Two types of condensing economizers are available: a standard one-stage condensing economizer, or a two-stage condensing economizer. In the two-stage system, the first stage is non-condensing and the second stage is condensing, so the system can heat two sources of water. Adding a condensing economizer increases energy efficiency between 4 percent and 8 percent.
- Increase efficiency with a Burner Replacement if your burner is operating with a dated linkage design, you can replace it with a high-turndown burner. Today’s high-efficiency burners increase the burner turndown rate and increase energy savings, because on-off cycles are reduced. Many times, high-turndown burners can work in conjunction with a multiple-boiler lead-lag control system, delivering even more energy savings due to an even further reduction in cycling.
- In addition, include Parallel Positioning actuators for fuel and air regulation, replacing single point positioning linkages. An efficient burner provides the proper air-to-fuel mixture throughout the full range of firing, without constant adjustment.
- A good O2 trim system will help regulate air damper or fuel valve to account for air changes in your boiler room providing energy savings.
- Adding Variable-Speed Drive (VSD) enables a motor to operate only at the speed needed at a given moment, rather than a constant RPM regardless of load demand. This speed variance results in the elimination of unnecessary electrical energy consumption because as the speed lowers, the power consumed decreases as a cube function of the speed. A VSD can be used on any motor but is commonly found on boiler feed and circulating pumps and
combustion air motors of more than 5 HP.
- The above component features are all integrated into Advanced Boiler Controls, a PLC-based platform incorporating burner management, combustion control and monitoring in one integrated package. By updating to this user-friendly intuitive control, more system data is available with better controllability. In turn this delivers better performance, enhanced safety, lower maintenance and reduced operating costs.
- A Steam Trap Survey is a review of your steam system to identify oversized, failing or leaky steam traps. Identifying faulty steam traps will cut energy waste and optimize your plant’s performance. A properly designed and maintained steam system will prevent valuable energy escaping and that’s money in the bank. Energy Control has proven experience with conducting steam trap surveys and provide a detailed report with key findings and recommendations.
- A Hybrid Boiler System combines condensing and non-condensing boilers. Non-condensing boilers are designed to operate at higher return water temperatures (above 130’), average 80 – 85 thermal efficiency and typically have a longer life. Condensing boilers can achieve efficiencies up to 98%, when the return water temperature is below dew point. When looking at the heating season, non-condensing boilers’ peak efficiency aligns with high-temperature applications when the winter season is in full force. Condensing boilers align with milder heating seasons just before and after the winter season. By combining non-condensing and condensing boilers in a hybrid boiler plant system, facilities can reset building set points and reduce fuel consumption and cost.
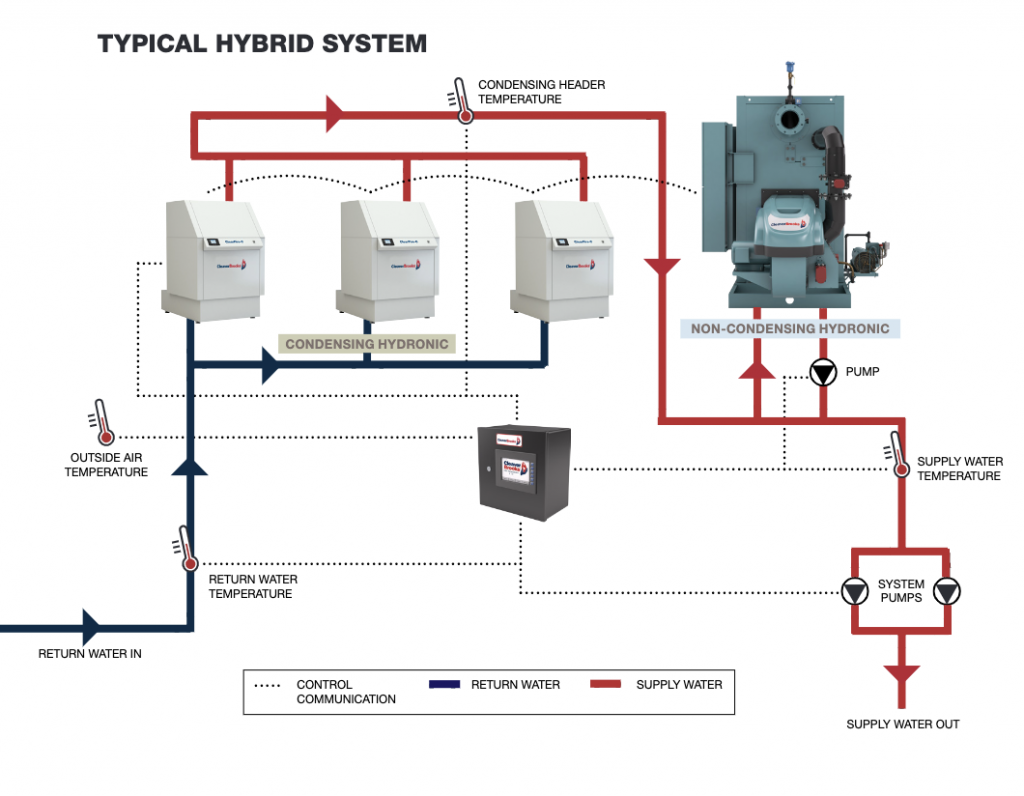
A Typical Hybrid System – Courtesy of Cleaver-Brooks
Building owners with an existing boiler can benefit from adding a smaller condensing boiler to avoid cycling during low-demand periods and operate at the most efficient point.
The ClearFire-CE is a high-efficiency condensing boiler option. It is a high-mass firetube boiler with up to 6,000 MBH input. Not only is it up to 99% efficient, it comes standard with less than 20 ppm NOx emissions.
Reduce Emissions
Reduce emissions and increase efficiency with a Burner Replacement if yourburner is operating on a linkage design, you can upgrade your burner to a high-turndown burner. Today’s high-efficiency burners increase the burner turndown rate and increase energy savings because on-off cycles are reduced. High Often, high-turndown burners can work in conjunction with a multiple-boiler lead-lag control system, delivering even more energy savings due to an even further reduction in cycling.
Contact us for a free boiler room evaluation to help uncover sustainable boiler plant options.